Computer
Engineering Department
Robotics
Laboratory
Professor Mayez Al-Mouhamed
Research Theme
Anthropomorphic Force-Reflective Master-Slave
System
Motivation
- A light, anthropomorphic,
back-drivable, transmission mechanism for telerobotics
- Fidelity and sensitivity
to small force/torque feedback magnitudes
- Effective mechanisms,
transparency, compactness, and low cost.
Approach
Figure 1: Anthropomorphic, 6 dof arm, without the driving cables
-
Multiple Loop Transmission
-
Multiple Cable Pulley Loop mechanism (simplicity, maintainability)
-
Each CPL is an independent system and can be locally maintained.
-
A loop starts with a threaded roller at motor shaft
-
Embedding the wire in the thread eliminates slippage
-
Both ends of the rope are wrapped around the driven wheel
-
Wire is wrapped 2 times to provide an acceptable range of motion
-
In the final wrap, the rope is restrained from any slippage
-
Pre-tensioning the wire is done independently for each loop
-
High-speed, low tension cable until the last transmission stage where a
high tension is used at the link level
-
Backdrivable Mechanism
-
Low gear, light mechanism, minimal friction
-
Decoupled rotative joints with no backlash due to the pre-tensioning
-
Reducers are placed as close as possible to driven links.
Fig.
2: Decoupled structure
-
Motor Grounding
-
All motors are grounded to improve arm dynamics.
-
Low friction cable routing structure within the first link for
uncoupling (dof 1 and 4)
-
The motor-link transmission is based on cable-pulley arrangement.
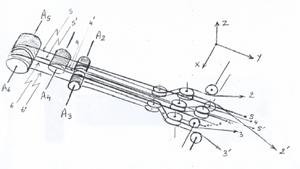
Figure 2: Threaded driving rollers and guiding system
-
Kinesthetic Force Feedback
-
Anthropomorphic: direct position-force mapping to human arm
-
Improved motion mapping: hand center at 3 concurrent rotation axes
-
Low friction, low inertia, uncoupled dofs (3 Kgs arm weight)
-
Kinematic model: rendering Cartesian position, display force, mapping
hand to remote tool.
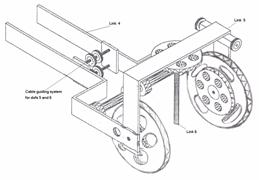
Figure 3: Hand center at the concurrency center of last three dofs