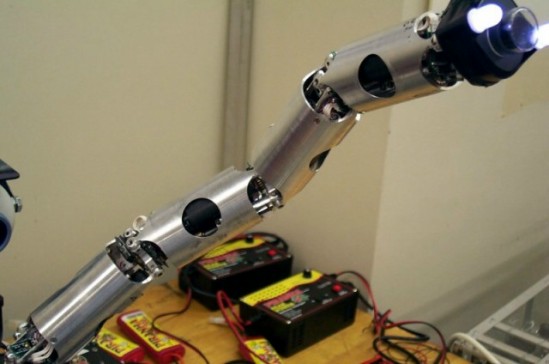 Snoopy, Double-Actuated Universal
Joint Robot
The simplest design that first comes to mind
is stacking simple revolute joints as close as possible to each
other and this led to the actuated universal joint design. As the
name suggests, he design incorporates a universal joint with two
motor to actuate each of the two degrees of freedom of the universal
joint. There are many variations of this design: The simplest of
which is just stacking revolute joint orthogonally and as close to
each other as possible, as seen in Figure 1. These kinds of designs
tend to be bulky and slow, hence not appropriate of lots of snake
robot applications.
|
Figure 1: Double
orthogonal revelute joint. |
Another varriation of this design approach is
by using bevel or worm gears train as seen in Figure 2 or using
push-pull rods, Figure 3.
|
Figure 2: Using
worm gears. |
|
Figure 3:
Push-pull design approach used in EOD snake
robot.. |
The main challange in this design approach is
to make the joint as compact as possible, yet strong enough and with
appreciable bending range. One of the main benefits of this design
is that you need only one motor to actuate one degree of freedom as
oposed to the rest of designs in the webpage where two motors are
actuated at all times. However, the torques transfered to the motor
are relatively larger hence the need of higher reduction. Usually
the high reduction is done by using power screws of worm gears hence
the slowness of the mechanism.
- Howie Choset: Advisor
- Elie Shammas: Graduate
Student
- Ben Brown: Idea, Design,
Engineering Drawings
- Al Costa: Electronics and PIC
programming.
- Sean Pieper: Electronics and PIC
programming.
- Electrical Engineering Shop:
Manufacturing
|